Cauchos sintéticos de uso general
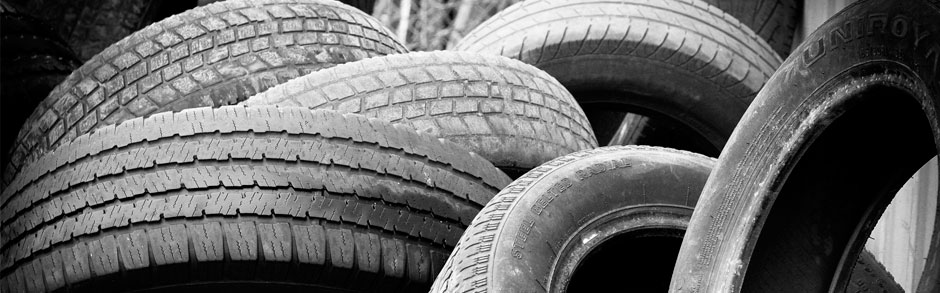
Los cauchos sintéticos se usan principalmente para aprovechar alguna de sus características especiales, que los hacen idóneos para aplicaciones determinadas como alta abrasión o baja permeabilidad.
Gracias al IR se logró obtener por síntesis un material homólogo al caucho natural y su formulación es muy similar a la de éste. En las operaciones de moldeo, tanto por compresión como por inyección, estos poliisoprenos sintéticos fluyen con mucha más facilidad que el caucho natural, lo que puede ser particularmente ventajoso en el moldeo por inyección o en la fabricación de piezas complicadas o de poco espesor y gran superficie; en cambio, su menor resistencia al desgarro, sobre todo a las temperaturas de vulcanicación, puede causar dificultades en el desmoldeo de tales piezas complicadas.
En la extrusión, calandrado y confeccion de artículos compuestos, los poliisoprenos sintéticos no presentan dificultades especiales, excepto las que puedan derivarse de su menor tenacidad y resistencia en crudo, y en el caso de los obtenidos con butil-litio, de su flujo en frío, La menor tendencia a la cristalización que poseen los poliisoprenos sintéticos se traduce en valores más bajos de dureza, rigidez, resistencia a la tracción y al desgarro, y por un menor índice de retención de estas mezclas sin cargas.
La mayor pureza de los poliisoprenos sintéticos da lugar a un mejor comportamiento como aislante eléctrico, así como a una menor coloración. Al tratarse de materiales sintéticos, presentan una uniformidad de características inalcanzables para el caucho natural.
Cauchos de Butadieno-Estireno (SBR)
Los cauchos de butadieno-estireno constituyen el tipo de caucho sintético de mayor volumen de consumo. Como el caucho natural, el SBR puede vulcanizar por medio de azufre y acelerantes, por medio de peróxidos o por medio de otros agentes vulcanizantes especiales.
El SBR es menos sensible a la oxidación que el caucho natural, en parte por llevar ya incorporado un antioxidante y en parte por su naturaleza intrínseca. Los SBR, además, necesitan de la presencia de cargas reforzantes para alcanzar un nivel satisfactorio de resistencia mecánica. Con tales cargas se obtiene una resistencia a la abrasión que frecuentemente supera a la del caucho natural.
Los cauchos SBR son claramente inferiores al caucho natural en lo que se refiere a resiliencia. En lo que respecta al comportamiento frente a la fatiga dinámica, los SBR son mejores que el caucho natural en cuanto a que tardan más en que aparezcan grietas, pero una vez iniciadas estas, por fatiga o por una eventual laceración mecánica, se propagan a mayor velocidad que en los vulcanizados de caucho natural.
En cuanto a sus principales aplicaciones destacan la fabricación de cubiertas de neumáticos, aislamiento de cables, artículos técnicos moldeados, calzado, correas, mangueras, o adhesivos, entre otros.
Los polímeros de butadieno figuran entre los primeros cauchos sintéticos fabricados a escala industrial. Cuando se emplea como único caucho en un vulcanizado, los BR de alto contenido cis-1,4 dan valores más altos de resistencia a la tracción y al desgarro, y de alargamiento en la rotura.
También es mejor su resistencia a la abrasión, que en todos los BR es superior a la del SBR y a la del caucho natural.
Una de las peculiaridades de los vulcanizados de BR es su elevada resiliencia, que a temperatura ambiente es superior incluso a la del caucho natrual. También es sobresaliente su resistencia al frío. Los BR de alto contenido cis mantienen su elevada resiliencia a temperaturas tan bajas como -40ºC.
Si en una formulación a base de caucho natural se sustituye progresivamente éste por BR, hasta que la proporción del último no supere un valor de aproximadamente 40-45 por ciento, no se produce un empeoramiento apreciable de las características de elaboración, y en cambio se obtienen las ventajas siguientes:
- Mejor resistencia a la abrasión
- Menor tendencia al agrietamiento por fatiga
- Mayor resistencia a la reversión
Análogamente, en el caso de una formulación a base de SBR, hasta que no se llega a sustituir aproximadamente el 50% del mismo por BR las características de elaboración no resultan afectadas de modo sensible, y en cambio se consigue:
- Mejor resistencia a la abrasión
- Menor tendencia al agrietamiento por fatiga
- Mayor resiliencia y menor histéresis, lo que se traduce en una menor generación de calor, y por lo tanto en menores temperaturas de rodaje